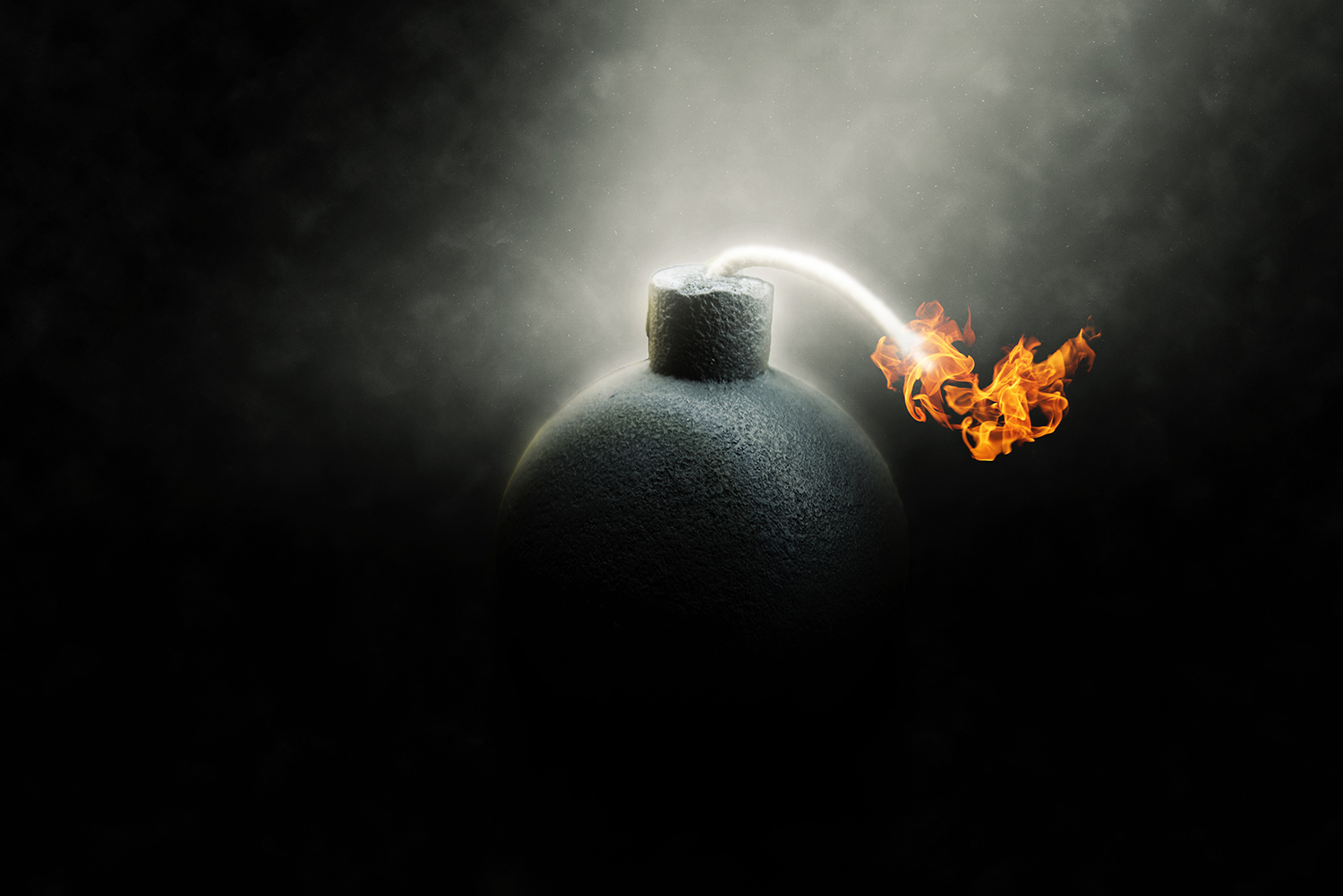
Anyone familiar with Marvin the Martian will remember one of his most famous quotes as he tries to blow-up planet earth: “Where’s the kaboom?”
There was supposed to be an earth-shattering kaboom!” Did this GSI webinar deliver that earth-shattering kaboom to the geosynthetics industry? Actually, I felt there were several. In this post let’s talk about the most significant.
This was the first GSI webinar that I personally attended and I thought Dr. Robert Koerner did an excellent job on the presentation, blending a heartfelt mix of brutal honesty with moments of humor. I felt the presentation had content relevant to all of us, whether you are new to the industry or a veteran seasoned with experience since the inception of geomembrane containment systems. This webinar itself has spurred so many items I would like to discuss or see studied at some point in the future – so it is sure to be an ongoing multi-series blog. I feel the best starting point for this series should begin with the biggest takeaway of all from the webinar – that Dr. Koerner’s recommendation on the acceptable height of waves/wrinkles is that they should lie flat.
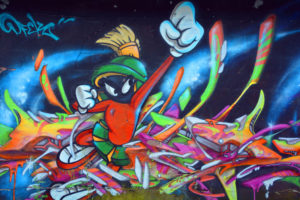
What would Marvin do?
Until recently, the general industry guideline has been that waves/wrinkles were acceptable if the height did not exceed two times the base width of the wrinkle (H < 2 x W) because such wrinkles would flatten out under the pressure/weight of the cover soils. Sometimes there was a maximum height specification and sometimes it was left at the discretion of the engineer. For anyone who never has experienced trying to measure developing wrinkles in the field – it is not the easiest thing in the world to do accurately!
Now, Dr. Koerner is recommending that the geomembrane should be flat before the first layer of soil goes on! Wrinkles as small as 14 mm have been shown to remain entombed in recent studies! In addition to being a violation of Federal and State regulations, entombed wrinkles have been shown to be a problem because they: create dams (I have argued this with many installers, engineers, and owners throughout my career); form a migration pathway and result in increased leakage rates of liquid and gas; and potentially decrease useful lifetime of the geomembrane (currently being studied by the GSI).
Kaboom! In case you missed it, this statement about having basically no waves in the geomembrane is earth-shattering news! Not because the news was unexpected, or perhaps long overdue, but because it truly alters the installation process as we now know it. With current installation and construction practices, it is relatively easy to mitigate wave/wrinkle size below 3-4” with nearly all materials – obviously there are a lot of variables at play including different material thermal expansion coefficients, different site conditions and restrictions, etc., but it can be done on a consistent basis. But, to take them down to zero – that is something where we really should stand back and take time to figure out how to achieve that goal.
My fear is the knee-jerk reaction that often comes when new data or recommendations are made available – everybody jumps on board with the latest and greatest and pens it into their regulations or specifications, without regard for how these specifications will impact the quality of the project, as well as the cost of the project. If the goal is to obtain zero waves/wrinkles, then we all need to stand back and figure out how to achieve this goal without compromising the integrity of installed liner systems, while minimizing the associated cost. What good is a liner with zero wrinkles if you’ve added hundreds, thousands, or even miles of extrusion welding (or perhaps other inferior repair weld types pending the material) to the project to fix wrinkles?
Why am I worried about the knee-jerk reaction? Because I think there are plenty of questions out there that need to be researched and answered before changing course. Here is a sampling of some of these questions:
- Besides thermal expansion and contraction, what other conditions lead to waves/wrinkles in geomembranes?
- Subgrade conditions?
- Friction interface of materials to subgrade, etc.?
- What happens to this friction after a geomembrane is placed on a CCL constructed wet of optimum and the daily heat draws moisture to the surface of the CCL underlying the liner?
- Equipment run on top of cover soil?
- I have seen liner installed flat, on near perfect subgrade, only to develop massive wrinkles from heavy equipment run on acceptable access ramps (4-5’ of granular fill over liner on ramp). The wrinkles took on the appearance of waves on a lake originating from the wake of a boat, with the “boat” being the access ramp.
- If it is possible that energy transfer results in waves/wrinkles, could the initial “select” lift placement during waste placement operations also result in waves/wrinkles?
- If so, who is liable?
- If it is possible that energy transfer results in waves/wrinkles, could the initial “select” lift placement during waste placement operations also result in waves/wrinkles?
- I have seen liner installed flat, on near perfect subgrade, only to develop massive wrinkles from heavy equipment run on acceptable access ramps (4-5’ of granular fill over liner on ramp). The wrinkles took on the appearance of waves on a lake originating from the wake of a boat, with the “boat” being the access ramp.
Additionally, Dr. Koerner provided several potential solutions for achieving zero waves/wrinkles. One of the methods presented is what he referred to as the “push/accumulate/cut/seam” method whereby cover is spread until a wave/wrinkle accumulates, then it is cut out and repaired, and this process continues until cover placement is complete. It is important to keep in mind several things regarding this option, even if it is used in conjunction with other options:
- A repair crew would need to be on standby throughout the entire cover placement duration.
- Repairs compromise the overall quality of the installation, and going to the repair method should be a viewed as a last resort.
- Where proper overlap is obtainable, fusion welds may be preferable over extrusion to minimize the amount of extrusion required (still need proper termination and extrusion patches at ends of fusion welds).
- It would be interesting to compare the decreased life expectancy caused by extrusion welding to that of the stress concentrations caused by waves/wrinkles.
- What CQA presence is required?
- The current trend is minimal (part-time or nonexistent) CQA presence on cover soil placement.
What questions do you have? As an owner, are you ready to pay for increased cost to mitigate waves/wrinkles?
The evidence presented may point to zero wrinkles as the best-case scenario, but we need to look at all facets of this issue. We must realize that our goal is to solve the core problems which may or may not include eliminating wrinkles. We will talk more about this in the future…
What I do know is that before we drop the “Zero Wrinkle” bomb and start writing new specs and regulations, we should make sure we’re not shooting ourselves in the foot. Otherwise, we may be no more successful than Marvin the Martian in his attempts to blow-up the earth. (You’ll have to watch some clips to see how that turns out if you do not already know.)
As an industry we must begin the dialogue to address known problems and I look forward to being a part of those conversations in the coming months!
Ian Peggs wrote an article in the GFR a long time ago that went something like this: “Wither did PVC go?”. Maybe we (you and Liz?) can talk Ian into writing another article on “Wither did the composite liner design engineer go?”. I have seen numerous lined process ponds, leach pads and containment dams throughout the world with so called “composite liner” designs in the mining industry. When pond liners have interconnected wrinkles above and below the water line (laterally and downslope) with ponds containing nasty caustic soda alkaline gold and silver solutions or highly acidic barren and pregnant sulfuric acid copper solutions, what was the design engineer thinking? For that matter, what were the landfill industry and EPA thinking over the years for containment of solid and liquid hazardous waste?
I have been an advocate for more flexible composite liner systems since I first designed liner for mining projects in the 1980s, and nothing I have seen or experienced over the years in more than 30 countries has changed my mind. I have written many articles about using less semi-crystalline liners for better load puncture resistance, interface friction strength and minimizing leakage, but it appears that I have been paddling upstream with a tooth pick for an oar! I like your discussions, and don’t worry about being “politically correct”. You will sleep better at night, cheers.
Glen,
Can you tell me if the panel raised any concerns with long term stress introduced by elimination of wrinkles?
It seems to me that by working to eliminate wrinkles we might also be introducing long term stresses should the solution be to pull the liner taut.
On past projects (with other materials) where a tight, wrinkle free condition was required we were only able to achieve this by incorporating a system of intermediate anchor trenches and repeated “pull-backs” during hot hours of the day with backfill in the early mornings or late afternoons.