We already are through the first full month of autumn, completing perhaps the busiest 12-month duration of my career.
Indeed, I am living the phrase “Time flies when you are having fun”! Some of the highlights of the summer include getting back out into the field for work, QA/QC training events throughout the United States, and being a lecturer at PeruMin 2015, the world’s largest mining convention. Each activity that I have been involved in has provided new opportunities to share with and learn from colleagues throughout the world and given me insight into topics needing further discussion. I look forward to sharing these topics with you over the next several months!
Continuity Testing vs. Integrity Testing
An important concept that even 25-year industry veterans continue to confuse: continuity testing is not a substitute for integrity testing! This is a topic that proves to be one of the biggest misconceptions I hear of in the industry, as well as one which I am frequently ask about, and even ask for clarification on. If you are working in this industry, it is important that you understand the difference between the two! Even if you are a 20-year veteran, I ask that you take a moment to read this series as a refresher. And, as always, I welcome any and all comments or questions!
As someone pointed out to me, a bridge is a great analogy in helping people understand the difference between continuity and integrity. Just because there is a continuous pathway over the valley below, it does not mean it will support the designed load.
In the context of geomembrane installations, continuity testing is a test that helps ensure there are no gaps (holes) in a seam or a panel, and most commonly, given the current available technologies used in the field at the time of this writing, is a non-destructive test performed on the seam or the panel. At best, these tests have minimal correlation to the overall integrity of the materials being tested. However, gleaning certain information from these tests can give an insight into areas that need more scrutiny.
In comparison, integrity testing is methodology used to primarily evaluate the strength of the material or seam as an indicator of long-term viability. For the geomembrane sheet, this process starts in the manufacturing process through certain tests performed on the resin, and continues through conformance testing of the final sheet, measuring many additional properties (to strength), which provide an indication of long-term viability. However, once the material passes conformance testing (MQA/CQA), commonly prior to shipment in today’s practices, what tests are performed after installation to ensure the material still maintains its integrity? What tests are performed to evaluate even a small portion of a panel considered suspect, perhaps due to blemishes, wind blowout, or other damages? A leak location survey is not going to provide this answer!
For instance, lets examine the two suspect panel areas mentioned above – blemishes and damages caused by a wind blowout. If either of these two damages has holes, the leak location has the potential to find them (I say potential, because there are a lot of contributing factors, such as hole size, and whether or not the survey is conducted on bare geomembrane or after cover has been placed). For the moment, let’s assume the blemished area causes an irregularity in thickness that was not detected in the conformance testing, even up to 90% loss of thickness (6 mils remaining on a 60 mil smooth sheet). Clearly, the affected area in this case no longer meets the specification, and the long-term integrity has been compromised. However, a leak location survey will not detect this flaw.
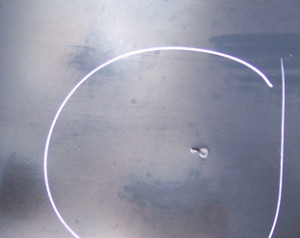
Umelted Resin Incorporated Into Finished Sheet
A different type of blemish is unmolten resin becoming incorporated into the sheet during the manufacturing process. While no hole exists, it is a structural flaw that in many instances needs to be repaired. Again, whether the area is vacuum tested or surveyed using an electrical leak location method, this damage will pass those tests because there is no hole, yet they compromise the integrity of the liner system.
Similarly, what is done to evaluate the creasing that often occurs when portions of panels are subject to wind damage, resulting in both thinning and structural damage to the geomembrane? Similar damage occurs when a hard object protruding from the subgrade below the geomembrane is stepped on, causing both thinning and structural damage to the geomembrane. If the damage does not fully penetrate the geomembrane, it will not be detected by most continuity test methods.
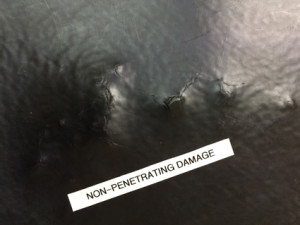
Non-penetrating Damage
In any of these instances mentioned above, the continuity test (leak location survey, vacuum box, etc.) is not going to detect these flaws – they need to be detected using good, old fashioned CQA, and can be tangibly confirmed using appropriate tests available in geosynthetic laboratories, should the need arise.
The same holds true for continuity testing of seams. Common methods such as the air pressure test of dual track fusion weld, and vacuum testing of extrusion welds will find leaks if properly executed by competent personnel, but they in no way validate the integrity of the seam (PVC dual track fusion welds tested by ASTM D-7177 being one accepted exception). The seam integrity is commonly evaluated by peel and shear testing, which is a destructive test used to validate seam strength.
Replacing Seam Destructive Testing with Leak Location Surveys
Based on discussions with numerous personnel in various positions throughout the world, there is an increasing thought trend moving towards writing regulations and specifications that replace seam destructive testing with leak location surveys. This is a dangerous road to head down!