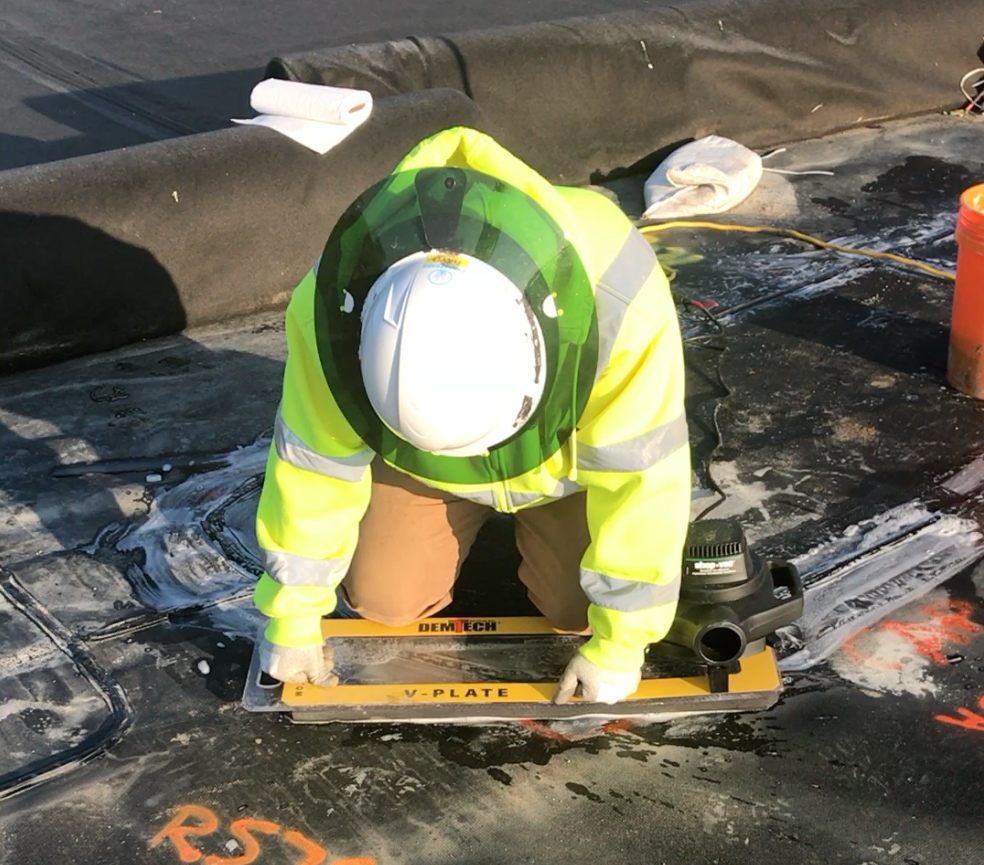
A quick test could save Millions of Dollars
Don Ho’s famous “Tiny bubbles… Make me happy” may be grand when it comes to love and Champagne but those pesky bubbles can leave site owners in tears when missed on a job site. The goal of Vacuum Boxing is to ensure the most technically difficult and error prone weld (extrusion welding) on site has solid continuity to the base substrate.
The destructive failure rates of extrusion welds can be up to 5 times greater than fusion welds in laboratory testing. Extrusion welding is often utilized in critical components of liner systems such as sumps and repairs. So solid testing protocols and execution are imperative. Yet, one of the most often overlooked aspects of a geomembrane installation is vacuum testing of extrusion seams.
This task is often viewed as one of the most mundane tasks and is assigned to “newbies”, both on the installation crew as well as for the CQA observation team. From a CQA perspective, it is relatively easy to tell when the vacuum box operator is not meeting dwell time and/or overlap requirements, proper pressurization, and even keeping the vacuum box clean.
But the question that often goes unasked is: “Does this operator know how to identify a leak?” This question should be asked BEFORE any vacuum testing is performed!
Ask that question to a vacuum box testing technician and you may be astounded! Over the past 5 years, we have regularly asked this question and in going through our notes, there is greater than 85% percent of technicians (ones we have not worked with before) performing vacuum box testing that had no idea what a leak looks like. The most common response when asked if they know what a leak looks like is: “I don’t know, I was told to run this machine over all the extrusion welds – that’s all.”
Here is a quick simple way we ensure that the QC/Testing Technician is adequately prepared for vacuum boxing. To combat poor quality on your projects, as well as provide education for the testing technicians, perform a blind leak test on scrap materials and have the vacuum box technician attempt to find the blind leak.
Blind Leak Test
- Select a sample testing material: whenever possible, use an extrusion trial weld for your test. If a scrap extrusion weld cannot be used, you can use a scrap piece of geomembrane. Extreme care must be taken to ensure this piece of geomembrane does not end up used as a repair.
- Puncture the geomembrane along the edge of the weld (or if the weld edge lifts up, underneath that edge) or somewhere on the geomembrane is a scrap pieces is being utilized. We have found that a thumbtack size hole is sufficient for a good blind leak trial. The testing hole should be fairly inconspicuous.
- Make sure the testing technician does not see where the hole is located.
- Require the technician to vacuum test the amended sample and find the leak location. They should not be be assisted during this process.
- If they cannot pass this test on the first attempt, a second attempt may be warranted especially if a difficult location was selected. However, failure of an obvious test or second test should disqualify them from vacuum boxing until further training and subsequent passing a completely new blind test have been achieved.
- Anytime equipment or personnel are changed out, a new test should be performed. This assures that both the equipment and the operator are functioning sufficiently.
Not only does the blind leak trial ensure the operator knows what a leak looks like, it also tests the operator’s methodology and equipment capabilities to help ensure that a leak can be found. It is important to note that most vacuum boxes are not tested on site nor do they have an industry calibration requirement.
While it is not foolproof, the vacuum box blind leak test is an important tool that should be utilized in/by the CQA Plan, Site Owners and QA Inspectors. This quick validation takes minimal time, cost little to nothing on your job sites, but can literally save you millions of dollars by avoiding project failures. As always in Geosynthetics – the devil really is in the details.