First, the answer to Vol. 6 (last week). Here are 14 things I noted, in order of occurrence.
- Dirt stripes. Dirt stripes negatively impact seam quality. Dirt stripe on top of geomembrane = matching dirt strip on bottom of geomembrane when water is involved. Some materials cannot be cleaned and need to be discarded.
- Cut in seam. Cut was made halfway up the slope to facilitate two operators welding the long run. Extension cord length, gauge and the number of connections is critical to maintaining consistent voltage during welding. Inexperienced installers may have opted to weld the entire slope and compromised seam quality. Inexperienced CQA, engineers, and site owners often miss the cord length issue.
- Upper seam welding information: machine, operator initials, start time and date on the liner. Machine settings are good as well but required less often.
- Dirt on top of the upper geomembrane. Best practice is to reduce anything that can negatively impact weld quality and cleaning all sheet surfaces helps. Remember, we can’t see the lower sheet bottom side during welding either.
- Brushing the seam interface. The operator brushes the lower sheet. The upper was brushed prior. CQA needs a vantage point that allows inspection of the seam interface prior to and during welding. Note: particles are being swept onto the geomembrane indicating the seam may indeed have residual dirt not removed by the brush.
- Larger particles brushed onto geomembrane. The size, shape, and material being brushed onto the geomembrane is unclear. If it is an angular rock, it will have the potential to damage the geomembrane and should be removed. Operators set such materials next to the seam but no one removes them, resulting in unnecessary damages when they get stepped/driven on or left on the geomembrane and covered.
- Brush drop. Nothing should be dropped on the geomembrane!
- Cord tension. Too much tension on cord. Too much tension impacts the machine movement.
- Stepping on the cut, monitoring lap, and assisting the machine to the end. Good practice: operator assured proper overlap through the end of the weld.
- Extension cord gets between rollers. Safety hazard!!! Can cord get to the wedge? It is dangerously close. If it does, heat will instantly damage the cord and significantly increasing the risk of fire and electrical shock!
- Cutting the machine out. Good: utilized a hook blade. Bad: blade not retractable. Hook was out while the operator wrestled the wedge. Bad: cutting towards his body instead of way.
- Setting the machine on geomembrane. Rub sheet should be used, even then, machine should be set down gently on the geomembrane. Rough handling can cause damage to geomembrane, and machine.
- Removal of geomembrane. Geomembrane cuts should be rounded/terminated with a circular cut. Scrap geomembrane must be secured to ensure safety.
- Operator wrote welding end time. Good! Initials and machine number even better.
As someone mentioned, I also would like an end bone.
In these blog posts, Do You See What Glen Sees, I will present a photograph or short video related to earthwork or geosynthetics construction and have you identify the significance of what you’re seeing.
It could be things being done correctly or incorrectly. Primarily, these will be things that impact quality.
In addition to my blog, I’ll post this content on X and LinkedIn. You can post your response on one of those two.
I’ll give you my thoughts on each photo or video when I post the next installment.
Do you see what I see? Or did you find something I missed? I’m excited to find out!
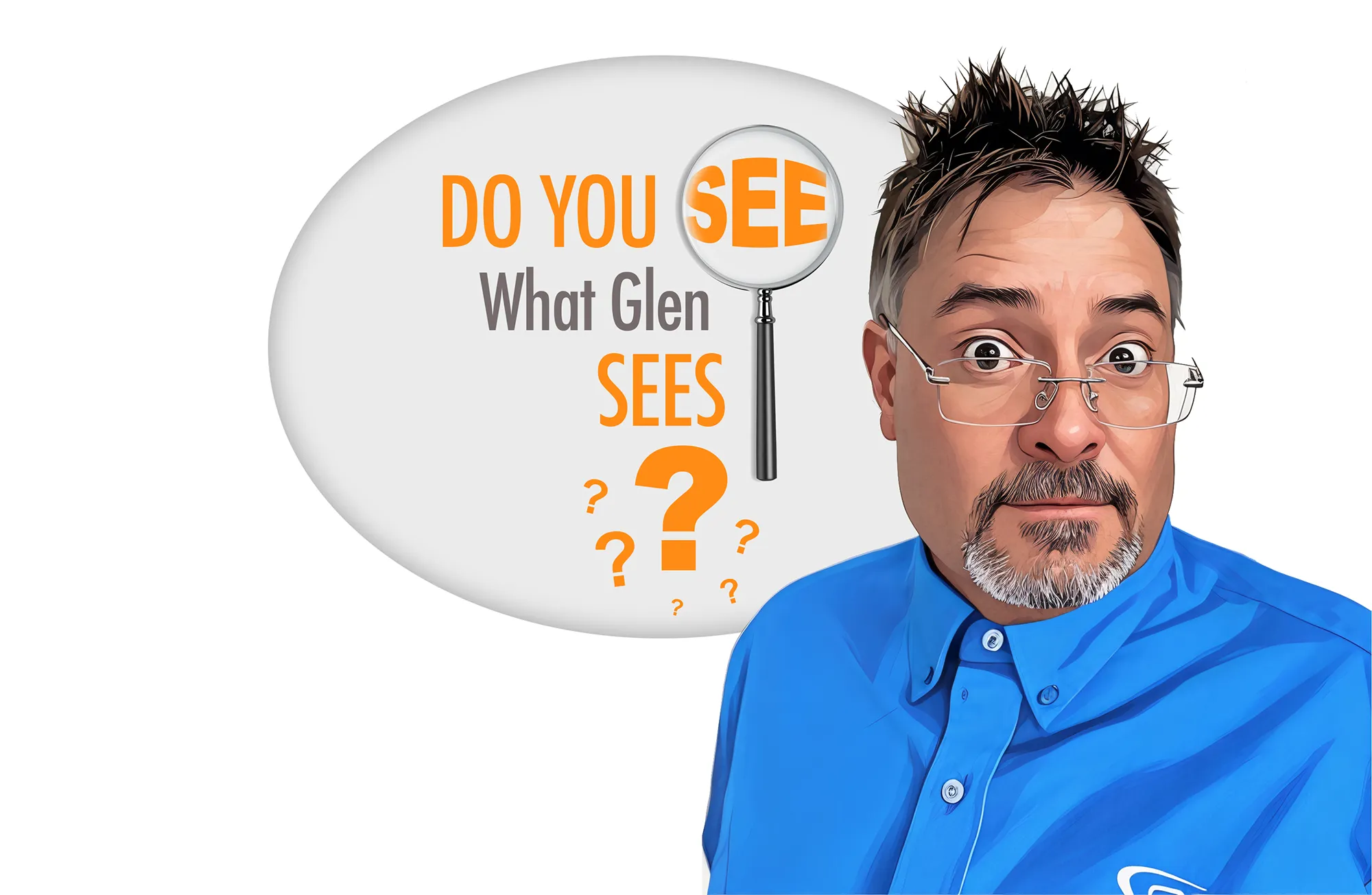
Here is the next installment. Take a good look. Do You See What Glen Sees?
It is becoming increasingly more obvious to me that pictures/videos I select because of one or two noted items often have many more things in them warranting discussion!
Things in the field often happen because poor construction documents restrict the ability of CQA/engineers to enforce best industry practices.
Enjoy!