Picture it – the Arizona Desert, June 15th 2011. A double-lined containment project encompassing nearly 200-acres.
You’ve been working night shift on a liner installation six-days a week since April and even longer on the project itself, with much more to come – night shift won’t end until at least late September.
At least in June the temperature drops down to a cool 100° F during the midnight lunch-hour!
You’re in charge of the CQA field staff and ultimately are responsible for ensuring the quality objectives of the project are met (which was zero-leaks). On a project of such magnitude, everyone is under scrutiny and the owner’s representative parked at the top of the slope every night was a constant reminder.
As many of you identified – it appeared there was tension on the project – a “healthy” tension was encouraged by the owner I later found out. You can be the judge of whether or not this was healthy, lol! Here’s what I remember happening…
I see an operator do something they shouldn’t do (they know they shouldn’t do it, the liner supervisor knows they shouldn’t do, everybody knows they shouldn’t do it) – in this case, I believe it was welding through chalk.
Normally, that’s something that gets written in my field book so when I am evaluating seams for destructive sample locations, I can refer to my notes and evaluate with other information such as air test results, etc.
Almost every time (99.9%), I don’t mark a destructive sample until after the air pressure test results are known, but in this case, I marked it right away! For those of you who know me, I walk every seam (sometimes two or three times) and take notes before marking my destructs.
I take this responsibility seriously, and if there is nothing suspect, I want to mark the samples where there is already going to be a hole. If there are multiple suspect areas, I want to compare them. So, my process takes time – it’s not merely putting samples every 500 feet.
But for some reason, I don’t clearly remember, I marked the sample immediately. If I recall correctly, I didn’t want to forget about it (that does occasionally happen even with the best of notes) and I needed to get up to the project trailer to catch up on paperwork.
Heck, I could blame it on the heat but that’s too easy of an out! For those of you who mentioned it, although not clear in the photograph, the sample is at the end of a fusion wedge welded tie-in seam of slope panels to floor panels (The sandbag is over the intersection hole). Fast forward an hour or two…
At the end of the shift, one of the CQA techs on the team comes up and tells me the installation supervisor wrote me a nasty note on the geomembrane and they were pretty sure I’d be upset.
I am sure it was on my mind trying to sleep that day and during my 45-minute drive back to the site. The project was always on my mind – I didn’t want to hear that they discovered a leak during the initial fill-up, or at any point beyond that!
And, l was blessed to have a liner foreman that felt the same way. We both were passionate about the quality of the work being performed, which really is expressed in his note back to me (although many may not see it that way).
When I finally walked up to the note, I just laughed. It probably was a relief given the anticipation of what I might find out there based on how the CQA tech made it sound. The absence of profanity in the note!!
Could I have handled it better ? Definitely! To ensure the situation was not escalated, I could have told the installation supervisor that I suspect that seam is bad and gone from there. In most instances, he would have investigated it upon my request (unlike many supervisors who tell me “throw a destruct on it and see.”)
There were many times I did inform him of my potential quality concerns and most of the time they were promptly addressed. As you can see, he already had figured out the seam was bad, maybe through end coupons, the air test or his own observations!
Now, I’d like to direct your attention to the seam overlap flap. As you can see, it has been trimmed off. I can assure you it was not this way when I marked the sample!
Basically, the installation supervisor was making sure the sample could not be destructive tested by removing the flap! This is something to keep an eye on when you are in the field.
Some welding technicians will trim the overlap flap off in areas they know are bad. That’s why I always recommend patching an area of seam where the overlap flap has been trimmed off or there is not enough to do a destructive test. Some CQA Plans and technical specifications have this requirement in there – many don’t. Add it if it’s not in there!
Additionally, I always give the installer the option to fix something rather than take a destructive sample. I don’t mind relocating destructs as long as things that look suspect are fixed.
BTW, we did successfully complete the various ponds to the zero-leak requirement – a requirement that was still met seven years after completion! (I’ve lost track of owner contacts after that.)
And despite some tense moments on site, the installation supervisor earned my respect – and that is saying something!
In these blog posts, Do You See What Glen Sees, I will present a photograph or short video related to earthwork or geosynthetics construction and have you identify the significance of what you’re seeing.
It could be things being done correctly or incorrectly. Primarily, these will be things that impact quality.
In addition to my blog, I’ll post this content on X and LinkedIn. You can post your response on one of those two.
I’ll give you my thoughts on each photo or video when I post the next installment.
Do you see what I see? Or did you find something I missed? I’m excited to find out!
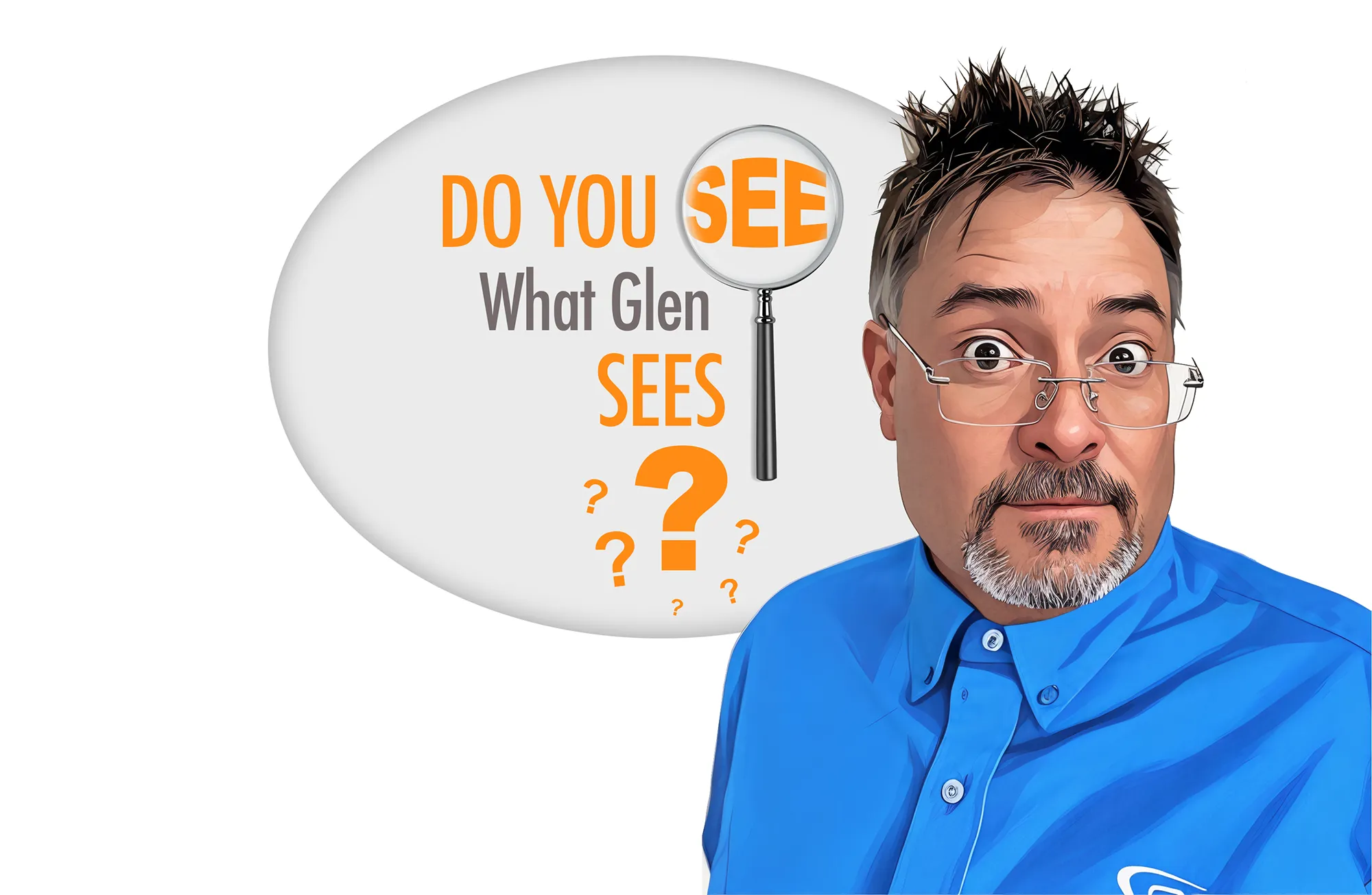
Here is the next installment. Take a good look. Do You See What Glen Sees?
Here is a fun video. If you want, you can restart it and have instant replay, LOL!
I did catch something I didn’t see the first couple of times, so let’s see if you catch it, too!
I look forward to your responses and perhaps an interesting discussion regarding this video as well.