I have to tell you that I am a fan of the bonded geocomposite products, especially those that combine geonet and geotextile into one unit.
Anybody who has been in the industry a long time, especially installers, may remember the tedious task of placing multiple layers of drainage/filter materials over the installed geomembrane. Admittedly, I was not a fan of some of the first bonded geocomposite products that I worked with, as the wind blew the geotextile right off the geonet, and the geonet frequently contained huge voids that could be seen through the composite and required repair; however, these problems seem to have primarily worked themselves out to where they are quite uncommon any more.
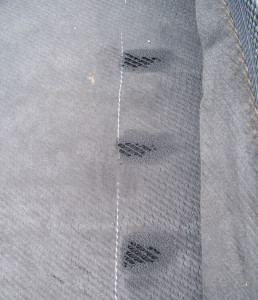
Burning holes through the geotextile layers is a quick way to prepare for geonet joining, but is it a safe and approved method?
(CLICK IMAGE for larger view.)
Double-sided bonded geocomposite products, particularly those with geotextile bonded to both the top and bottom of a geonet, pose a significant challenge for the installer–how to join the geonet layers with cable ties through the multiple layers of geotextile. Most manufacturers of the geotextile-geonet-geotextile bonded composite product leave a portion of the edges (approximately 6 inches) of each roll loose (not bonded), so joining the geonet layers here is not too hard typically. This is not the case if the panel is trimmed in the width direction, or for butt-seams. The installer must potentially deal with separating the bonded materials, which can be quite labor intensive, especially on butt-seams or odd configurations which usually have an increased tie spacing requirement (commonly side seams are spaced at 5 foot maximum intervals; butt-seams may require spacing at 6 inch or 1 foot intervals, and even multiple rows at that spacing).
Many installers have realized that one of the quickest ways to perform the preparation is to use heat to melt the geotextile–primarily the use of a propane torch, as the flame, if done efficiently, the heat will melt through both layers of geotextile in a second or two. Such a short burst of flame also gives the visual appearance that the geonet remains undamaged (whether this is true or not, I do not know, nor have I seen specific data on this but it is another thing to be considered in allowing this process). A longer application of heat will start to visually melt the geonet at which point the installer could be required to place a patch containing geonet over the damaged area. I have not found guidance on this issue in manufacturers installation manuals, installer manuals, or elsewhere.

Burning holes with a propane torch without lifting the bottom sheet off the geomembrane.
(CLICK IMAGE for larger view.)
Obviously, using a flame on geosynthetics has its own set of risks–including damaging the geomembrane below the geocomposite. When using this method, it seems appropriate that the materials should be lifted off the geomembrane during the burning process. However, this is often not the case, as the installer will argue that there is no way to align the holes between the layers–I usually suggest ways I believe it could be done. One such suggesting is completing the top sheet holes and overlapping onto the lower sheet, then using a marking implement such as sharpie marker, or even paint to provide the location on the bottom sheet, which would then allow the bottom sheet to be pulled up and burned without the risk of damaging the underlying geomembrane.
Unfortunately, I have yet to see where an installer will go to this amount of trouble, even after the geomembrane is damaged multiple times during the installation process! Therefore, my compromise is that I get to inspect all the holes before they are tied and covered up–with decent lighting, you can see some of the damage to the geomembrane, especially holes; however, I am unconvinced that a person can see minor damages that may normally be repaired if the observation was not impeded. However, in some instances the damage is obvious, such as when you turn around and the geocomposite is on fire–after the installer walked away! Unfortunately, I could not locate photos of this–and it has happened more than once!
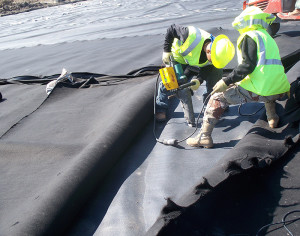
Installer repairing holes in geomembrane caused by the burning process.
(CLICK IMAGE for larger view.)
As one of my colleagues pointed out as we discussed this issue, it is amazing what is either allowed to occur or overlooked during work performed over top of the geomembrane that would be a no-no during the geomembrane installation. This may be a good idea for a future blog post! As an example we discussed, smoking on the geomembrane is forbidden (rightfully so), yet open flame is allowed literally inches from the geomembrane that has minimal chance of being inspected again.
What are your thoughts on allowing the flame burning technique to be used for textile-net-textile bonded geocomposite seaming? Does anyone have any data on whether the geonet is harmed during the flame process, and if so, is it relevant? Likewise, is there potential damage to the geomembrane that also may not be visible to the human eye? I am interested in hearing your experiences on this type of product, especially other seaming options that you may have found to be successful!
Also, how much CQA attention do you give to geocomposite installation? I am aware of instances where the CQA coverage is part-time at best during the installation, meaning CQA personnel may not even inspect the geocomposite on a daily basis.